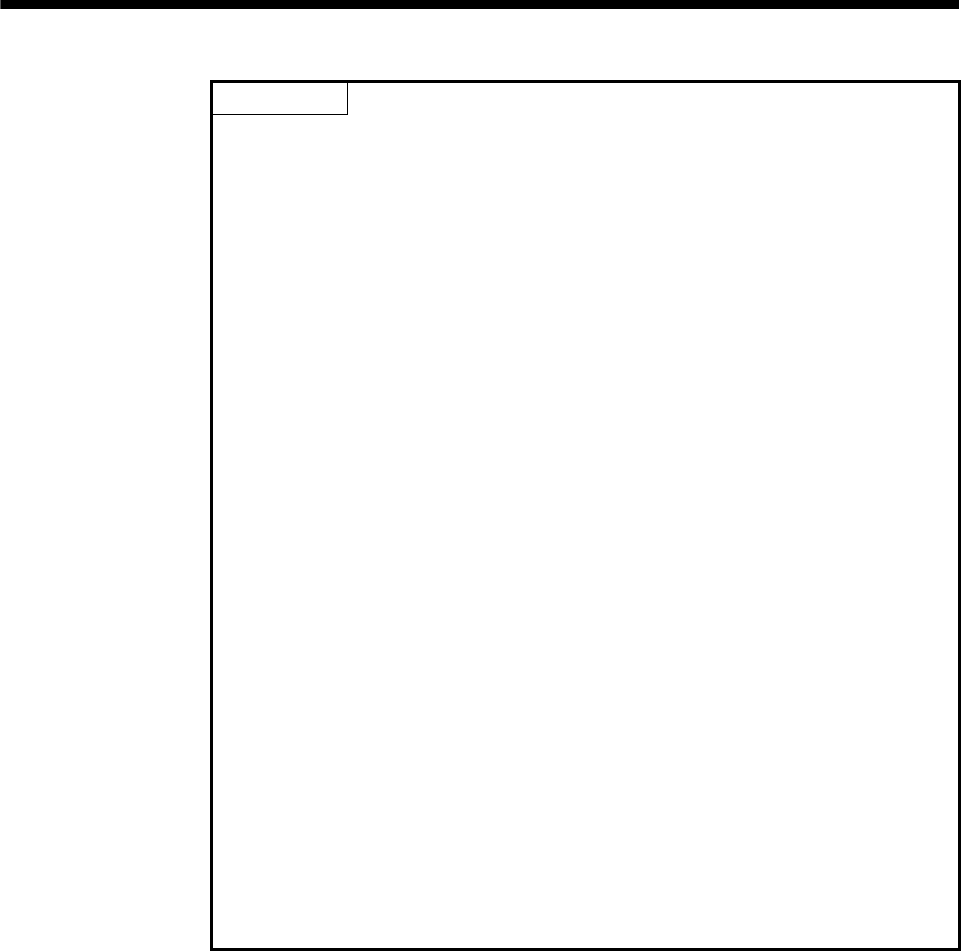
6 - 142
6. APPLICATION FUNCTIONS
POINT
• For all patterns, the control mode is automatically changed to position control
by the position board after zero speed (ZSP) turns ON.
• The stopping process for each stop factor is a deceleration process in
continuous operation to torque control mode. (For immediate stops, control
mode switches to position control mode at the current position and stops
immediately.)
• The time constant at a rapid stop is that of rapid stop time constant (control
parameter No.0227).
• The press limit position is determined by the current feedback position. The
position after a stop is a position exceeding the press limit position. Therefore,
a position that takes into account the operation after exceeding the press limit
position should be set.
• The software limit is determined by the current feedback position during
continuous operation to torque control. As there is a possibility of stopping at
a position that exceeds the software limit, set the press limit position before
the software limit. When the software limit is set before the press limit
position, continuous operation to torque control error (operation alarm 5D,
detail No.05) occurs, and operation does not start.
• If interlock (ITL) turns ON during position control mode for points with
continuous operation to torque control set to valid, continuous operation to
torque control error (operation alarm 5D, detail No.04) occurs.
• The interference check standby is invalid during position control mode in
continuous operation to torque control points.
• The above also applies when a stop factor occurs during switching to
continuous operation to torque control mode.
• An immediate stop occurs when a stop factor occurs during switching to
position control mode from continuous operation to torque control mode.