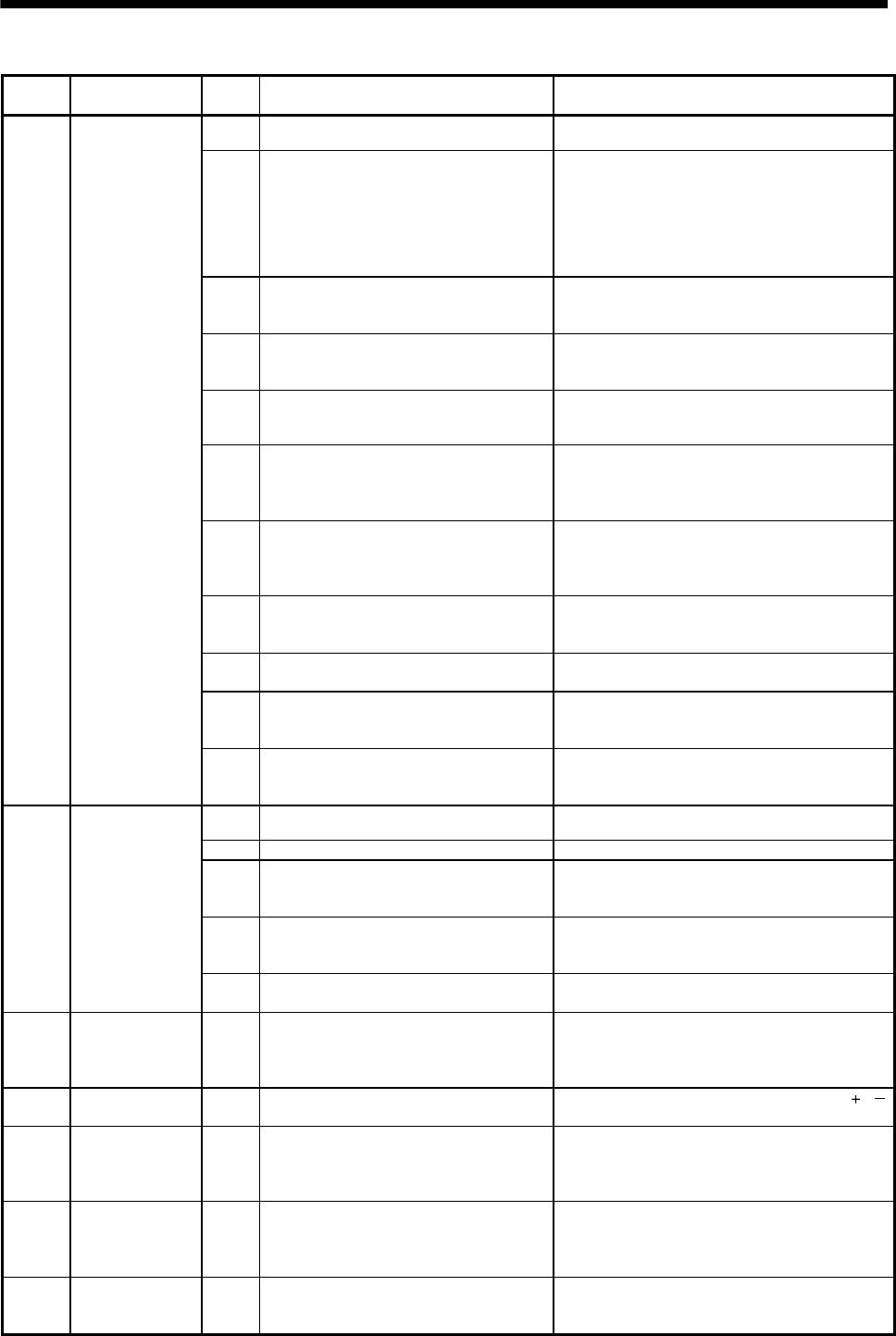
13 - 8
13. ALARM NUMBER
Alarm
No.
Content
Detail
No.
Cause of occurrence Procedure
5D
Continuous
operation to
torque control
error
01
Continuous operation to torque control
valid was specified to a tandem drive axis.
Specify continuous operation to torque control
invalid to the tandem drive axis.
02
When operating at a continuous operation
to torque control point, the operation was
completed without conducting a switch to
continuous operation to torque control.
(1) For automatic switch, reexamine the setting of
the continuous operation to torque control
switching position.
(2) For manual switch, conduct a switch to
continuous operation to torque control mode
before position control mode operation is
completed.
03 The press limit position was reached.
Reexamine the positions of the pressing position
in continuous operation to torque control and the
press limit position.
04
Interlock command (ITL) turned ON during
the operation of a point set to continuous
operation to torque control valid.
Do not input an interlock command during the
operation of a continuous operation to torque
control point.
05
The travel direction and press limit position
were incorrect.
(1) Reexamine the set values of the point table.
(2) Travel in the opposite direction, and start
operation before the press limit position.
06
A continuous operation to torque control
point was specified for a connected
module that does not support continuous
operation to torque control.
(1) Reexamine the set values of the point table.
(2) Use a servo amplifier that supports continuous
operation to torque control mode.
07
The control mode switch command
(CTLMC) turned ON during movement in
continuous operation to torque control
mode (before reaching target torque).
Turn ON control mode switch command after
completion of continuous operation to torque
control. (Switch to position control mode)
08
The press limit position was set to a
position before the position data of the
point table.
Set the press limit position to a position after the
position data of the point table.
09
The software limit was set to a position
before the press limit position.
Set the press limit position to a position before the
software limit.
0A
Continuous operation to torque control
valid was specified to a linear interpolation
axis.
Specify continuous operation to torque control
invalid to a linear interpolation axis.
0B
Continuous operation to torque control was
specified as valid for a point where travel
amount is 0.
Set the required travel amount in order to conduct
continuous operation to torque control.
5E
Continuous
operation to
torque control
setting error
01
Continuous operation to torque control
speed limit value is outside of range.
Reexamine the setting of the continuous operation
to torque control speed limit value.
02 Target torque is outside of range. Reexamine the setting of the target torque.
03
Continuous operation to torque control
acceleration time constant is outside of
range.
Reexamine the setting of continuous operation to
torque control acceleration time constant.
04
Continuous operation to torque control
deceleration time constant is outside of
range.
Reexamine the setting of continuous operation to
torque control deceleration time constant.
05
Continuous operation to torque control
operating conditions is out of range.
Reexamine the setting of continuous operation to
torque control operating conditions.
90
Home position
return not
complete
01
Automatic operation, linear interpolation
operation, or home position reset were
performed without executing return to
home position.
Execute home position return. Or validate no
home position (parameter No.0200).
91
Z-phase not
passed
01 The Z-phase has not been passed.
Turn the motor more than 1 revolution in the
/
direction and then perform home position return.
92
The proximity dog
is short
01
When using dog method home position
return, after the dog turned on and
decelerating to a stop, the position is not
above the dog.
Lengthen the proximity dog. Or in order to stop on
top of the dog, reduce the home position return
speed.
94
Home position
return direction
error
01
The home position return direction and
stopper method direction are opposite
when using a stopper method for return to
home position.
Set the home position return direction to be the
same as the push direction.
95 Not limiting torque 01
"Torque limit effective" has not been turned
on when stopper method is being used for
return to home position.
Perform push, and after torque limitation effective
state, perform start operation for home position
return.