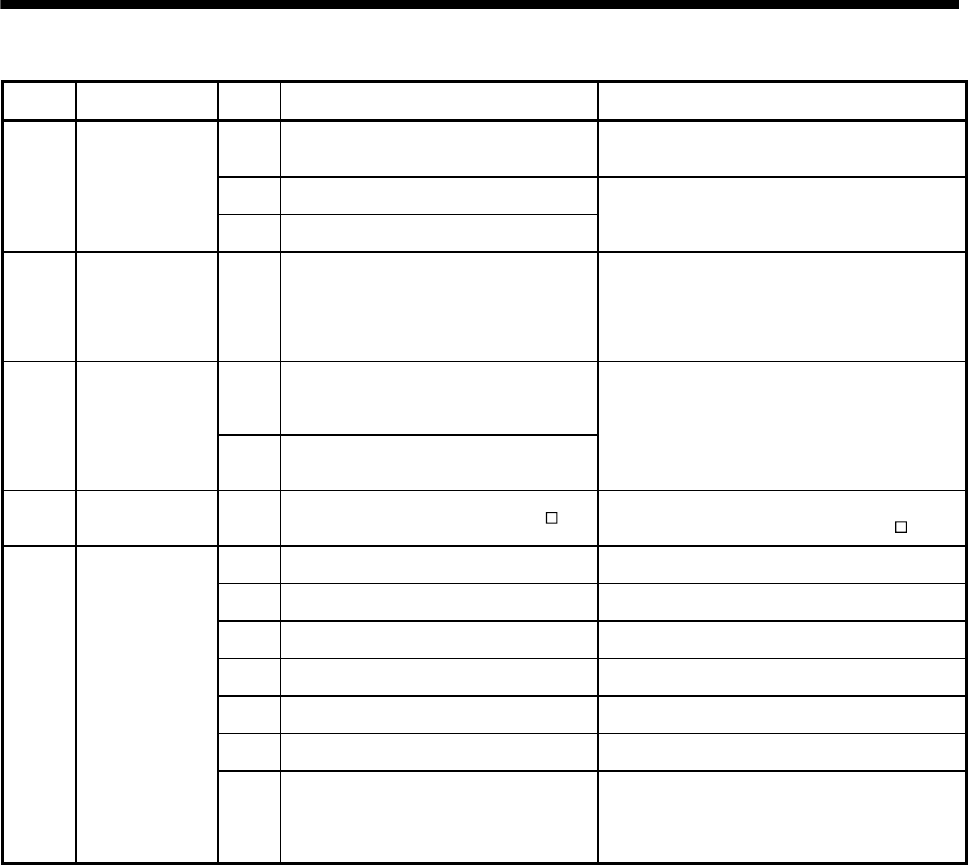
13 - 7
13. ALARM NUMBER
Alarm
No.
Content
Detail
No.
Cause of occurrence Procedure
56
Tandem drive
slave axis error
01
There is a servo alarm for the parallel drive
slave axis (including servo warning E6, E7,
E9).
Cancel the servo alarm. For details, refer to the
Servo Amplifier Instruction Manual on your servo
amplifier.
02
A communication error or a power outage
on the servo amplifier occurred.
Confirm that the connection to the servo amplifier
is intact. Reference system errors in the system
status code for details concerning communication
errors.
03
The tandem drive slave axis entered servo
ready off mode.
57
Exceeding of valid
width of tandem
drive deviation
compensation
error
01
The deviation between the master axis and
the slave axis exceeded the valid width
when home position return was performed
while in tandem drive mode.
(1) Adjust the mechanical deviation between the
master axis and the slave axis so that it is
within the valid width.
(2) Set the tandem drive home position signal
offset (parameter No.026C, 026D) to a correct
value.
58
Tandem drive
synchronous
alignment error
01
When a stop command is input during
calculation error correction performed for
turning on the servo, while in tandem drive
synchronous mode.
To correct the error between the master axis and
the slave axis, turn the servo off and then on to
perform synchronization again.
02
In tandem drive synchronous mode, the
start operation is performed without
completion of synchronization.
5B
Using other axes
start data
01
Other axes start data is being used (the
other axes start notice signal (OSOP ) is
on).
Check the other axes start data is not being used
(the other axes start notice signal (OSOP
) is off).
5C
Pass position
interrupt error
01
The setting to the start number of the pass
interrupt condition is out of range.
Check the start number setting of the pass
interrupt condition.
02
The setting to the end number of the pass
interrupt condition is out of range.
Check the end number setting of the pass
interrupt condition.
03
The start number of the pass interrupt
condition exceeds the end number.
Check the start number setting and the end
number setting of the pass interrupt condition.
04
The setting of the pass interrupt condition
is out of range.
Check the pass interrupt condition setting.
05
The specified pass interrupt condition is
used for other axes.
Do not overlap the pass interrupt condition
numbers for each axis.
06
The operation is started during the pass
position output interrupt.
Do not start the operation until the pass position
output interruption is completed.
07
During the pass position output interrupt
cancel signal (PPISTP) is on, the operation
is started with setting valid to the pass
position specification for auxiliary
command of point table.
Start the operation after turning off the pass
position output interrupt cancel signal (PPISTP).