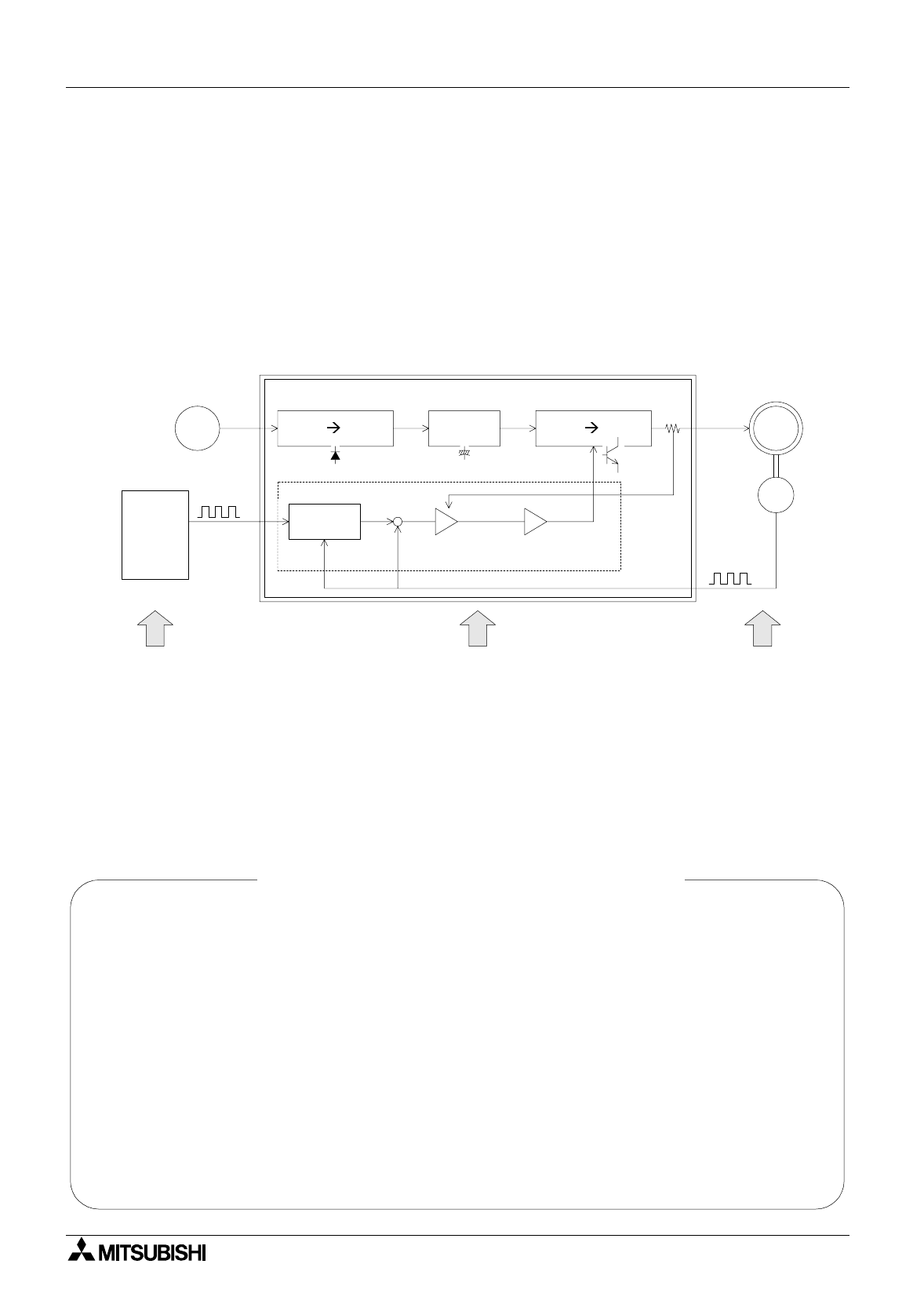
Positioning by AC Servo System 2
2-1
2. Positioning by AC Servo System
2.1 When an AC servo system is introduced
• Positioning can be performed by many diversified methods. Recently, AC servo methods
which offer many advantages are often introduced.
• In the positioning system of an AC servo method, a position controller, servo amplifier and
servo motor are generally required. The representative system configuration is shown
below.
Position
controller
Deviation
counter
DC ACDCAC DC
Converter
Smoothing
circuit
Inverter
PWM (pulse width
modulation) control
Current
control
Speed
command
Feedback
current
PLG
SM
Feedback
pulse
Encoder
Servo
motor
Command
pulse
Servo amplifier
The position controller
generates a specified
quantity of forward rotation
(or reverse rotation) pulses at
a specified frequency.
The command pulse number
is subtracted by the feedback
pulse number, and the speed
command to drive the servo
motor is made from the
deviation (accumulated pulse
number).
When the accumulated pulse
number becomes 0, the servo
motor stops.
The servo motor is equipped
with a built-in encoder (pulse
generator), dedicated to high
speed response, and suitable
to positioning control.
Commercial
power supply
The AC servo system satisfies the needs for
multi-model small-lot production through only
simple changes in the program.
AC servo systems are easier to handle than
hydraulic equipment.
As an AC servo system can generate large
torque, it can satisfy the needs for down sizing
and high power.
- Release from oil management
Robots in conjunction with an AC servo system
can satisfy the needs for labor saving and
automation.
- Release from dangerous, hard and dirty
working environments
Why is the AC servo system attracting attention?
Positioning Control