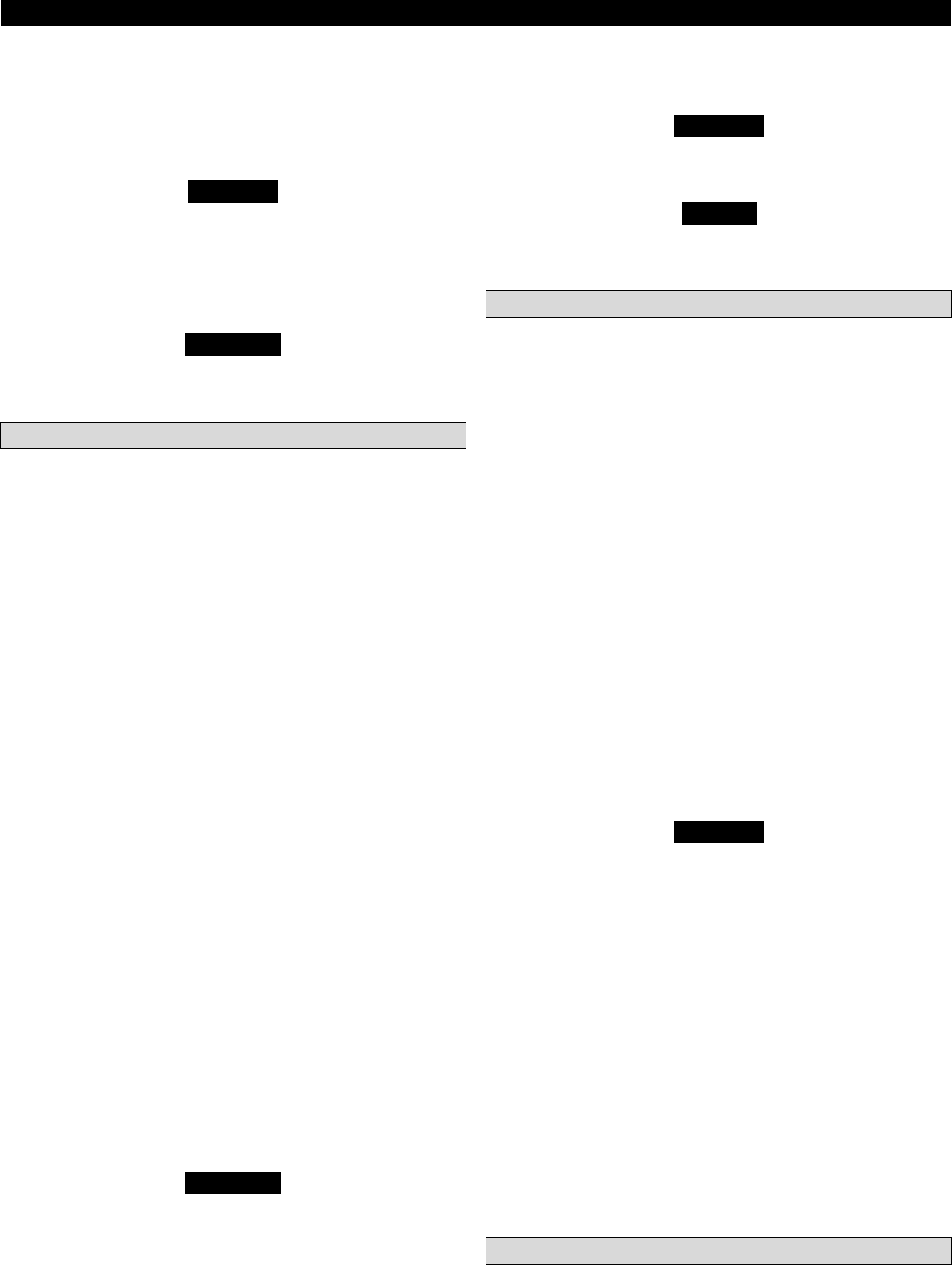
5
INSTALLATION
Prior to installing the hoist, carefully inspect it for possible
shipping damage.
Hoists are supplied fully lubricated from the factory.
Lubrication of the load chain is recommended before initial
hoist operation.
CAUTION
• Owners and users are advised to examine specific,
local or other regulations, including American National
Standards and/or OSHA Regulations which may apply
to a particular type of use of this product before
installing or putting hoist to use.
WARNING
• A falling load can cause injury or death. Before
installing, read "Safety Information."
Mounting
Make certain your hoist is properly installed. A little extra
time and effort in doing so can contribute a lot toward
preventing accidents and helping you get the best service
possible.
Always make certain the supporting member from which
the hoist is suspended is strong enough to support the
weight of the hoist plus the weight of the maximum rated
load plus a generous factor of at least 500% of the
combined weights.
If the hoist is suspended by a top hook, the supporting
member should rest completely within the saddle of the
hook and be centered directly above the hook shank. Do not
use a supporting member that tilts the hoist.
Hook Mounted Hoist
Place hook over mounting structure. Make sure hook latch
is engaged.
Trolley Mounted Hoist
When installing a trolley on a beam, measure the beam
flange and temporarily install the trolley on the hoist to
determine the exact distribution and arrangement of the
spacers. The total distance between the wheel flanges
should be 3/16 in. to 1/4 in. (4.76 mm to 6.35 mm) greater
than the width of the beam flange.
The number of spacers between the trolley side plate and
the mounting lug on the hoist must be the same in all four
locations in order to keep the hoist centered under the I-
beam. The remaining spacers must be equally distributed on
the outside of the side plates. (For additional information
refer to the trolley manufacturer's literature.)
WARNING
• At least one mounting spacer must be used between
the head of each trolley bracket bolt and the trolley
bracket and between each trolley bolt nut and the
trolley bracket. Failure to do this could cause the hoist
to fall when used improperly.
Ensure the trolley bolts or nuts are torqued in accordance
with manufacturer's specifications. When installing the
hoist and trolley on the beam, make certain the side plates
are parallel and vertical. After installation, operate the
trolley over the entire length of the beam with a capacity
load suspended 4 to 6 inches (10 to 15 cms) off the floor.
CAUTION
• To avoid an unbalanced load which may damage the
trolley, the hoist must be centered under the trolley.
NOTICE
• Trolley wheels ride on the top of the lower flange of
the beam.
Air System
The supply air must be clean, lubricated and free from
moisture. A minimum of 90 psi (6.3 bar/630 kPa) at the
hoist motor is required to provide rated hoist capacity. Air
inlet port size for LCA015S and LCA030D units is 1/2 in.
BSP. On all other units the inlet port size is 3/4 in. BSP.
Air Lines
The inside diameter of the hoist air supply lines must not be
smaller than 3/4 in. (19 mm). Before making final
connections, all air supply lines should be purged before
connecting to system inlet. Supply lines should be as short
and straight as installation conditions will permit. Long
transmission lines and excessive use of fittings, elbows,
tees, globe valves, etc. cause a reduction in pressure due to
restrictions and surface friction in the lines.
Lubricator
The air motor may be operated without lubrication. If an air
line lubricator is used, it should be replenished daily with
SAE 30W Grade ISO VG 100 oil (minimum viscosity 135
Cst at 104° F (40° C)).
CAUTION
• Shut off air supply before filling air line lubricator.
Filter
It is recommended that an air line strainer/filter be installed
within 3 ft (1 m) of the motor air inlet port to prevent dirt
from entering the motor. The strainer/filter should provide
20 micron filtration and include a moisture trap. Clean the
strainer/filter monthly to retain its operating efficiency.
Moisture in Air Lines
Moisture that reaches the air motor through the supply lines
is the chief factor in determining the length of time between
service overhauls. Moisture traps can help eliminate
moisture. Other methods, such as an air receiver which
collects moisture before it reaches the motor or an
aftercooler at the compressor that cools the air prior to
distribution through the supply lines are also helpful.
Motor
For optimum performance and maximum durability of
parts, operate the air motor within the operating
specifications provided in the "SPECIFICATIONS"
section. The air motor should be installed as near as
possible to the compressor or air receiver.