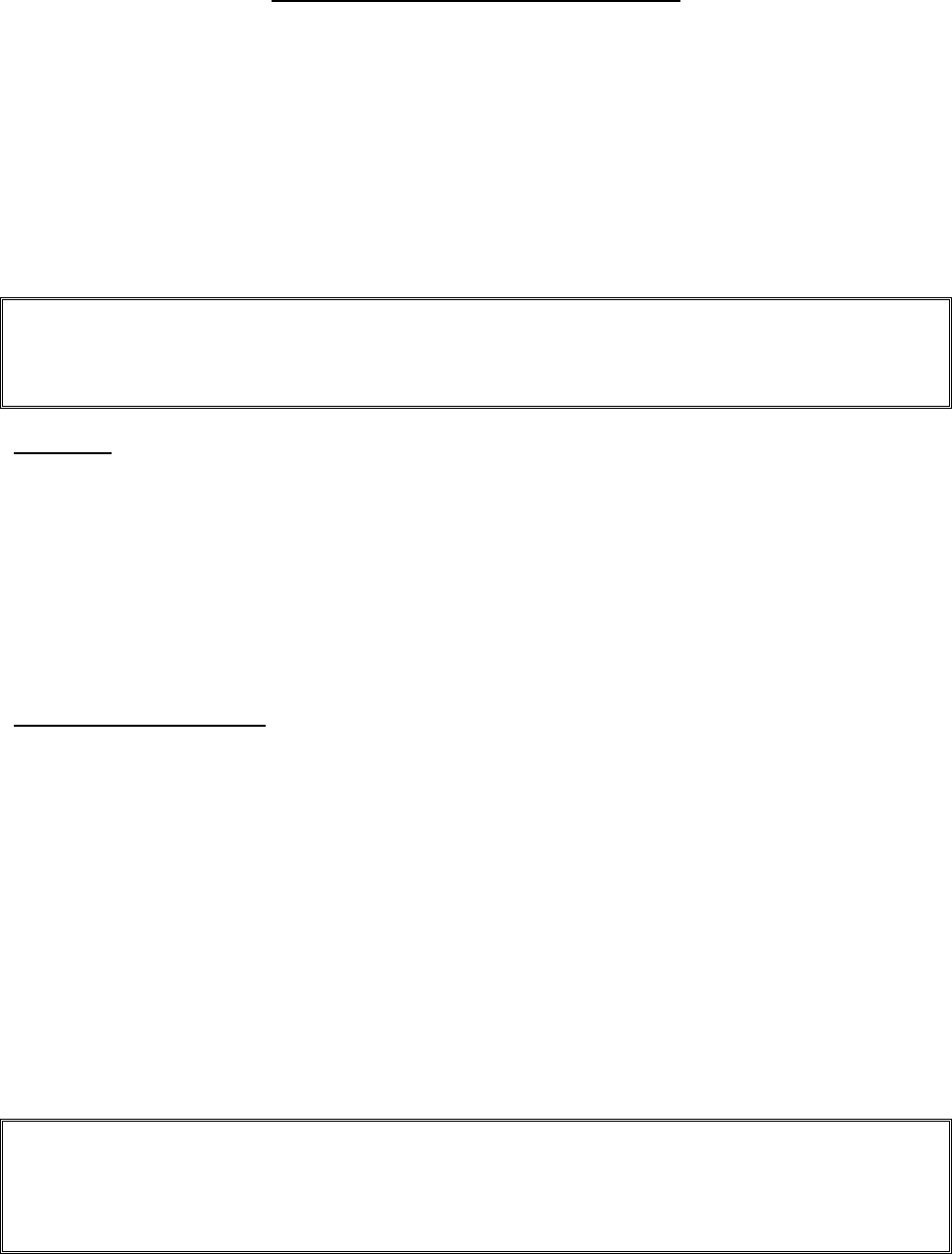
T O L E R A N C E S A N D W A R N I N G S
Allegro ambient air pumps are precision pumps that have only .0015-.003 clearance between the top of the rotor and
cylinder bore, and .003 or less clearance between end of the rotor and the end plate. Any thrust on the shaft such as
mishandling or dropping the pump on its end will tend to close these clearances, causing the rotor to jam. Foreign
particles, excessive dirt or dust build up may cause sluggish performance and eventual “jamming” of the pump. The
pumps have carbon vanes and grease packed bearings. They MUST NOT be lubricated or flushed with petroleum
base solvents.
All models have precision ground vanes inside the pump that take up their own wear and will last approximately
3,000 hours, depending upon workload, maintenance, speed and degree of pressure. Excessive dirt, foreign
particles, or moisture could cause the vanes to stick in the rotor slots and even break. Periodic “flushing” could
prevent this. Use the Allegro flushing cleaner (P/N: 9700-65) in the pump chamber only.
CAUTION!
The basic materials used in the pumps are cast iron and steel. Consequently, any moisture will tend to corrode the
interior, especially when pump stands idle for extended periods.
AIR PUMP: (9850)
o The motor for the Air driven pump is a precision built rotary-type motor. The vanes for this motor take up their
own wear and will last 5,000 to 15,000 hours depending upon speed, operating pressure, and the precautions
taken in maintaining the motor.
o The type of shaft seal used does not lend itself to operating pressures above 100 psi (6.89 bar).
o The air motor requires a minimum of 75 cfm at 80 psi inlet pressure and volume to operate pump.
o The starting torque is less than the running torque and could vary depending on the position at which the vanes
stop in relation to the air intake port.
o The speed and torque can be regulated by using the pressure regulator or shut-off ball valve to obtain desired
power.
EXPLOSION PROOF PUMP: (9833)
• The Ambient air pump is rated for use in hazardous locations, however the user must ensure that the following
guidelines are followed:
o The inlet filter (or Extension) must not be in a hazardous environment; this will endanger the respirator
user. Inlet filter must be in a clean uncontaminated environment at all times.
o Testing of ambient location where inlet filter is placed is strongly recommended, to ensure it meets CGA
specifications of grade D or higher.
• The pump is rated to be used in the following hazardous locations:
o Class I, Group D
o Class II, Group F and G
• Verify your location classification.
o Ensure the pump design meets the hazardous class and group classifications of job site.
o The National Electric Code divides these locations into Classes and Groups according to the type of
explosive gas/agent, which may be present.
o For specific information, consult the National Electric Code, Section 500.
• The Hazardous Location plug and receptacle must be used to hardwire the pump to the power source. Consult a
qualified electrician and the National Electric Code articles 500 through 517.
CAUTION!
Hazardous location equipment may be required in any area where the presence of flammable gases, vapors or finely
pulverized dusts in the atmosphere is sufficient to create a threat of explosion or fire. It may also be required where
easily ignitable fibers of flyings are present.
4